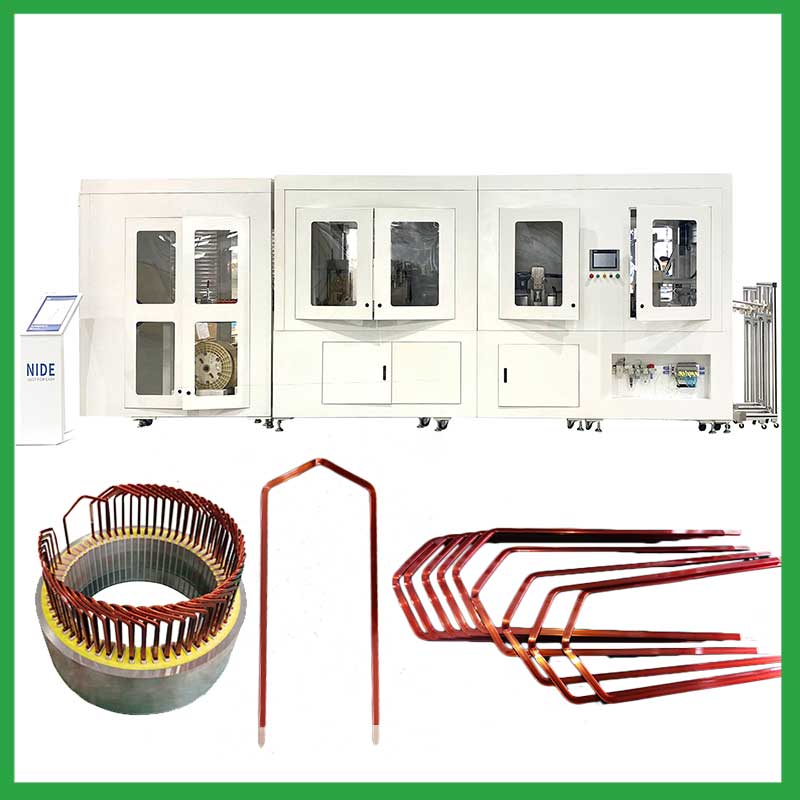
Automatic Hairpin Stator Forming Machine Hairpin Technology Motor Winding Solution for Automobile
Model number:ND-HPML-ST030
Introduction:The main function of the hairpin forming machine is to remove the paint, bend and form the flat copper wire, and finally fold it into a fixed hairpin shape. It is one of the most critical equipment in the entire hairpin motor stator assembly line.
- Specification
Automatic Hairpin Stator Forming Machine Hairpin Motor Technology Solution for Automobile Drive Motor
The hairpin coil forming machine can manufacture various U-shaped hairpin designs of different designs. It is assembled in the electric drive stator and is a special equipment for the forming and processing of hairpin coils of new energy drive motors.
Since the stator copper wire winding of the flat wire motor is a flat thick copper wire, the stator wire package cannot be formed by winding like round copper wire, and must be processed one by one through a forming machine. After the hairpin is formed, the hairpin wires are inserted into the stator core in groups, and finally assembled into a finished motor stator through equipment such as flaring, twisting, welding and varnishing. The main function of the hairpin forming machine is to remove the paint, bend and form the flat copper wire, and finally fold it into a fixed hairpin shape. It is one of the most critical equipment in the entire hairpin motor stator assembly line.
Hairpin Stator Forming Machine Process description
The main structure includes: wire feeding mechanism, straightening mechanism, punching and paint removal mechanism, wire release mechanism, cutting mechanism, hairpin coil forming mechanism, waste suction mechanism, wiring mechanism, etc.;
The hairpin stator forming machine is started manually, and the machine automatically completes material unloading, copper wire straightening, punching and paint removal, fixed-length feeding, 2D forming, cutting, 3D forming, waste suction, stamping and forming, and hair pin collection.
Manual loading and unloading of copper wire coils,
Automatic forming by machine,
Manual replacement of molding molds.
The hairpin stator winding process is divided into 5 steps:
•Unwinding copper wire from coil, straightening and feeding into the station
•Remove insolation from wire at certain positions
•Cutting wire pieces to certain required lengths
•Bending 2D forms
• Forming 3D shapes with one installed forming die, flexible to exchange for different forms
Hairpin winding technology advantages:
The symmetrical and sturdy shape of hairpin windings makes them easier to wind than round wires, greatly simplifying assembly.
Unlike round wires, hairpin coils can be precisely positioned, allowing for a cleaner design.
Hairpin windings can carry more current than round wires. Higher efficiency results in less heat generated by the windings and motor. This simplifies temperature management and improves motor reliability and life.
Due to the higher filling factor, the additional copper creates a stronger magnetic field. This allows the rotor to spin stronger and the wheels to have more torque. A better filling factor means the stator can be smaller.
Energy losses when current passes through copper (called copper losses) are minimized. This is due to the optimized winding path (all winding turns are the same shape and symmetrical).
The motor can use less energy to produce the same power, which helps extend the vehicle's mileage.
Round wires require stitching to hold the windings together (a process called stator braiding), which hairpin windings do not require.
Hairpin motors have a lower risk of long-term failure. This is because their conductors are larger, stronger, and less affected by vibration.
Quality Control of Hairpin Forming Technology
1. Servo wire feeding system, wire feeding accuracy can meet ≤±0.2mm; 2. The deviation between the U-shaped shape size after forming and the theoretical digital model: the straightness of the leg is ≤0.2, the crown including R and the contour 20mm below the crown is ≤1; 3. The 2D bending angle accuracy is ≤0.5°; 4. The breakdown voltage of the U-pin line is not less than 90% of the copper wire withstand voltage requirement (the withstand voltage value needs to be verified in practice); 5. The U-pin has no abnormal bending, deformation or interweaving; 6. There is no residue at the paint removal, and the thickness is uniform; About NIDE
Nide is to provide different kinds of motor manufacturing machinery, including stand along machine, fully-auto complete line for armature and stator production, and the motor assembly line.We can supply the full range of motor components such as commutator, ball bearing, carbon brush, insulation paper, shaft, magnet, fan, motor cover,etc.We also provide technical support and consulting, project support and turn-key service for some motor manufacturing.
Our machine's application
Our machines are mainly applied to hairpin motors, induction motors, BLDC motor, universal motor, three phase motor, single phase motor, AC motor, DC motor, such as washing machine motor, air conditioner motor, pump motor, cooler motor, alternator motor, fan motor, ceiling fan motor, compressor motor, power tool motor, vacuum cleaner motor, mixer motor, series motor, electrical car motor, wheel hub motor, electric toothbrush motor, hair dryer motor, electric shaver motor,etc.
Contact us
Motor Manufacturing Solution
Email : emarketing@nide-group.com; marketing8@nide-group.com;
SNS