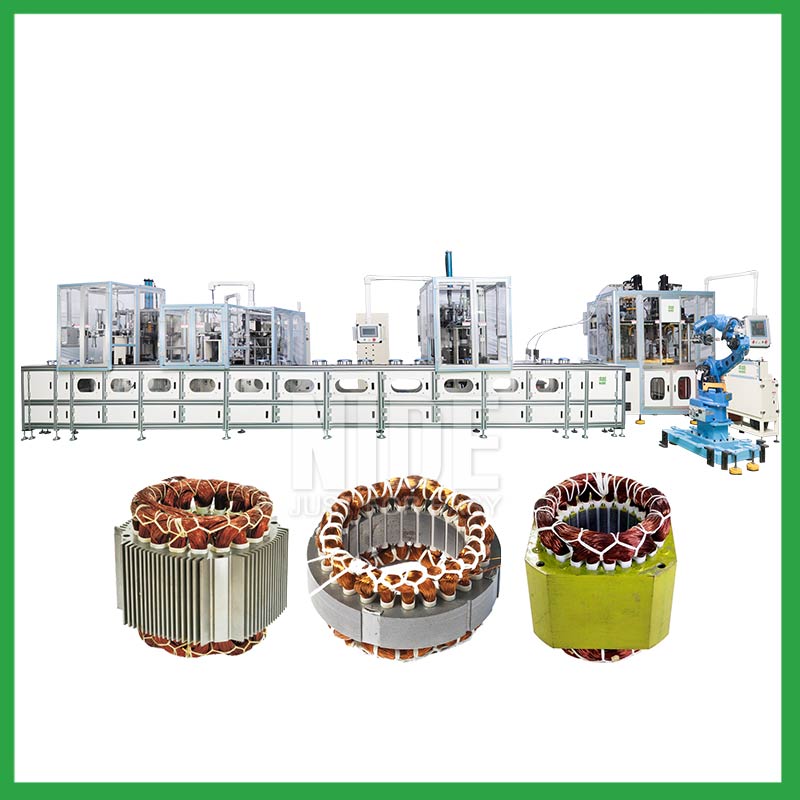
Fully Automatic Three-Phase Motor Stator Production Line with Remote App Control
Model number:ND-DZXSJ
Introduction:This fully automatic three-phase motor stator production line with mobile app control is engineered to boost productivity, precision, and automation in motor stator manufacturing. Designed for applications such as washing machine motors, table fan motors, and small industrial motors, this line integrates advanced machines for paper inserting, coil winding, lacing, and forming—delivering high-efficiency stator production with minimal human intervention.
- Specification
Fully Automatic Three-Phase Motor Stator Production Line with
Remote App Control
The Fully Automatic Three-Phase Motor Stator Production Line offers a cutting-edge solution for
modern motor manufacturers seeking automation, efficiency, and scalability. The integration of mobile
app-based remote control enables real-time monitoring and operational adjustments from anywhere,
enhancing flexibility and ease of use.
This automated line is especially suitable for high-volume washing machine stator assembly, table fan
stators, BLDC stators, and other three-phase motor stator applications.
Key Features & Advantages
Fully Automated Workflow: Includes insulation paper inserting, coil winding and inserting, lacing,
and forming—streamlining production and reducing labor dependency.
Mobile App Control: Enables remote monitoring, fault diagnosis, and real-time parameter settings
via smartphone.
High Production Efficiency: Optimized for mass production with fast cycle times and minimal downtime.
Precision Manufacturing: Servo-driven systems ensure coil accuracy, clean insertion, and consistent quality.
Customizable Operation: Parameters adjustable per stator model through a user-friendly HMI interface.
Production Process Flow
Slot Paper Inserting Machine
Inserts insulation paper into stator slots with high precision.
Coil Winding and Inserting Machine
Performs automated coil winding and insertion, supporting parallel wires and multiple pole configurations.
Stator Coil Lacing Machine
Secures the windings using Mylar wedges with programmable spacing.
Stator Coil Forming Machine
Shapes the stator to exact specifications without damaging the winding.
Technical Specifications
Flyer Swing Diameter: 240mm
Stack Length: ≤90mm
Stator Outer Diameter: ≤150mm
Winding Speed: ≤2200 RPM
Number of Wire Jumps: 2-4 sections
Wire Diameter: 0.18-1.2mm
Parallel Winding Wire Number: ≤2
Air Pressure Requirement: 0.5 ~ 0.6 MPa
Power Consumption: 14kW
Machine Weight: 4000kg
Operating Temperature: -10°C to 60°C
Machine Dimensions: 2700mm (L) × 2300mm (W) × 2200mm (H) (including wire barrel)
Machine Components in Detail
1. Automatic Stator Coil Winding and Inserting Machine
Three winding stations, each independently controlled.
AC servo motor for precise indexing, wire cutting, and paper feeding.
Cam divider for rapid and accurate coil insertion.
Parallel winding without damaging enameled wire.
XY-axis movement for wire hooking and cutting.
2. Automatic Coil Lacing Machine
Servo-driven wedge paper feeding for consistent lacing.
Adjustable wedge length and slot spacing.
Built with hardened steel for durability and accuracy.
3. Automatic Coil Forming Machine
High-precision shaping with damage-free insertion.
Pre-deceleration and speed control features.
Real-time monitoring and automatic wire break detection
Applications
This production line is ideal for:
Washing Machine Motor Stators
Table Fan Motor Stators
HVAC Compressor Stators
BLDC Motor Stators
Industrial Pump Motor Stators
Why Choose NIDE?
As a ISO-Certified Motor Manufacturing Solutions Provider, NIDE delivers:
Turnkey Projects: From stator lines to full motor assembly systems
Global Support: 24/7 technical consulting & spare parts logistics
Component Ecosystem: Commutators, bearings, shafts, and insulation materials
Watch YouTube Demo Video
About NIDE - Your Reliable Partner in Motor Manufacturing Equipment
NIDE Group specializes in the R&D and manufacturing of motor production machinery. We offer a full range
of solutions including standalone machines, fully automatic production lines for armature and stator, and
complete motor assembly lines. With over a decade of experience, we support clients with high-efficiency
equipment and tailored automation solutions for various motor types.
Our product portfolio also includes motor components such as commutators, ball bearings, carbon brushes,
insulation paper, shafts, magnets, cooling fans, and motor covers. In addition, NIDE provides technical consulting,
project design, and turnkey services to help clients optimize their motor manufacturing processes.
Machines Application
NIDE machines are widely used in the production of various motor types, including:
AC motors / DC motors / BLDC motors / universal motors / induction motors
Single-phase and three-phase motors
Common application fields:
Household appliances: washing machines, air conditioners, vacuum cleaners, electric mixers,
electric shavers, hair dryers, electric toothbrushes
Industrial equipment: pumps, compressors, power tools, fans, coolers
Automotive: electric vehicles, hub motors, alternators
NIDE helps manufacturers build efficient, automated motor production lines for both high-volume
and customized projects. More information please check our New Website: www.nidegroup.com.
Global Service & Support
NIDE offers global installation support, training, and after-sales services. Our engineering team ensures
smooth machine integration and continuous production performance. Contact us for technical consultation
for guidance on equipment selection.
Contact Us
marketing8@nide-group.com (Head of Electric Machinery and Equipment)
emarketing@nide-group.com (Head of Motor Parts)
SNS